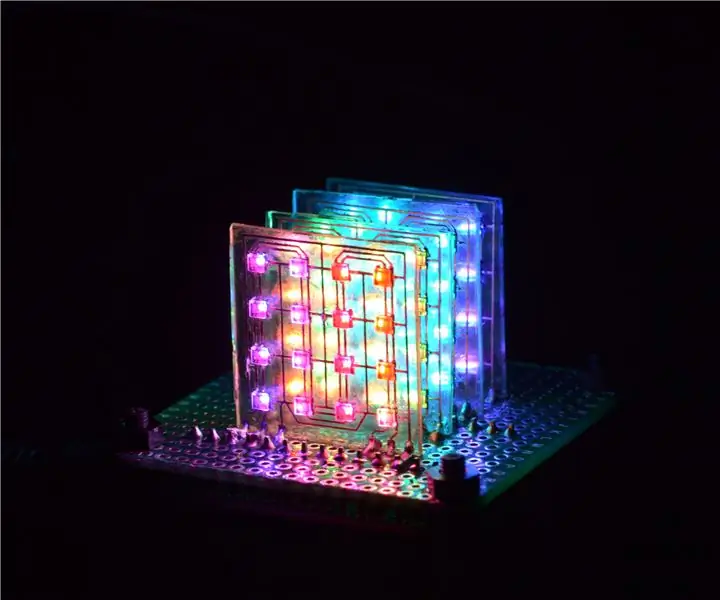
תוכן עניינים:
2025 מְחַבֵּר: John Day | [email protected]. שונה לאחרונה: 2025-01-23 14:46
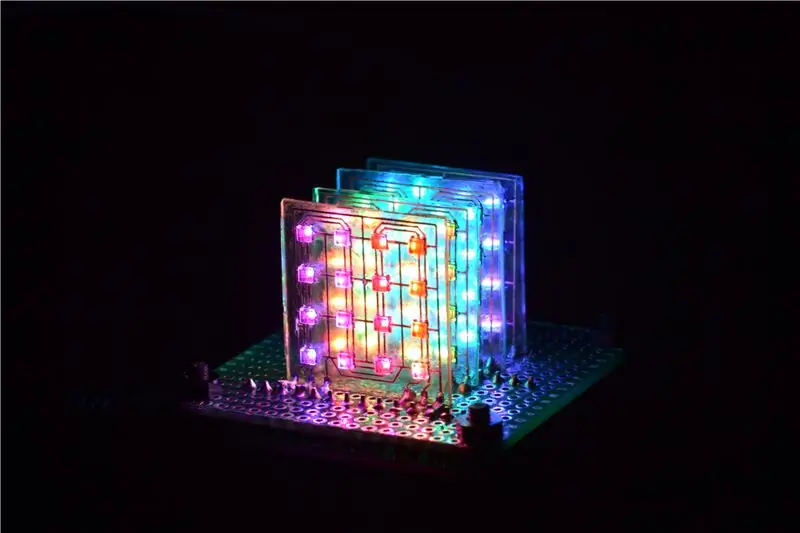
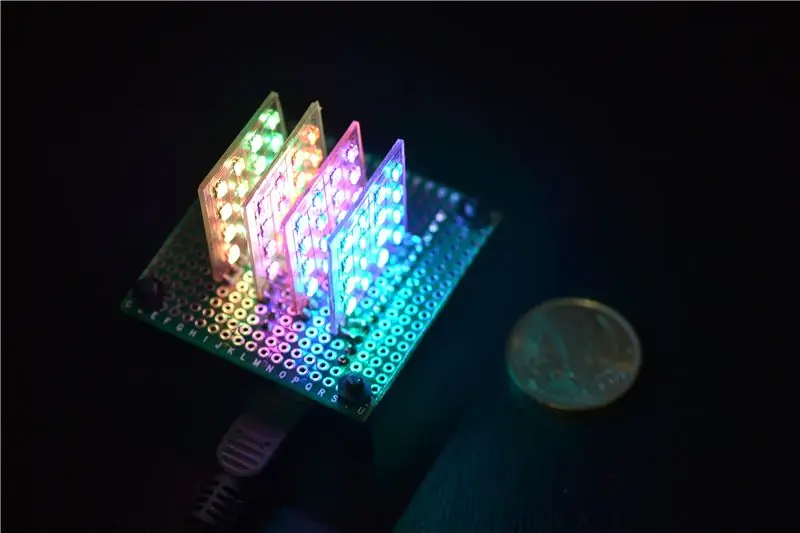
ההשראה לפרויקט הזה באה מקוביות LED קטנטנות אחרות כמו של HariFun ושל nqtronix. שני הפרויקטים הללו משתמשים ב- LEDs SMD לבניית קובייה בעלת ממדים ממש קטנים, אולם נוריות ה- LED הבודדות מחוברות באמצעות חוטים. הרעיון שלי היה במקום זאת להרכיב את הנורות על לוח PCB, כפי שנועד לחלקי הרכבה על פני השטח. זה גם יפתור את הבעיה של סידור הלדים בצורה מדויקת במטריצה עם אותם מרחקים שיכולים להיות לעתים מסובכים בעת חיבורם באמצעות חוטים. הבעיה הברורה עם PCB היא שהם אטומים ולכן השכבות הבודדות יוסתרו זו אחר זו. כשגלשתי באינטרנט עם זה בחשבון, נתקלתי בהוראות CNLohr כיצד להכין PCB מזכוכית שקופה. כך עלה לי הרעיון להכין קובייה קטנה מנורות SMD המותקנות על גבי PCB זכוכית. למרות שזו לא קוביית ה- LED הזעירה ביותר בעולם (הכותרת הזו כנראה עדיין שייכת ל- nqtronix), אני חושב ש- PCBs הזכוכית מוסיפים נופך חדש ונחמד למגוון הגדול של קוביות LED שכבר קיימות.
שלב 1: כתב חומרים
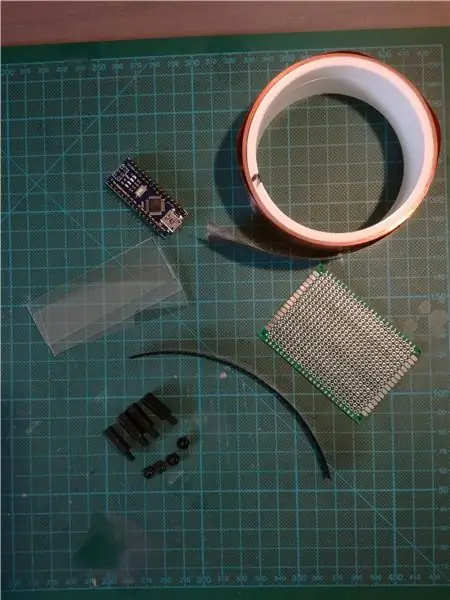
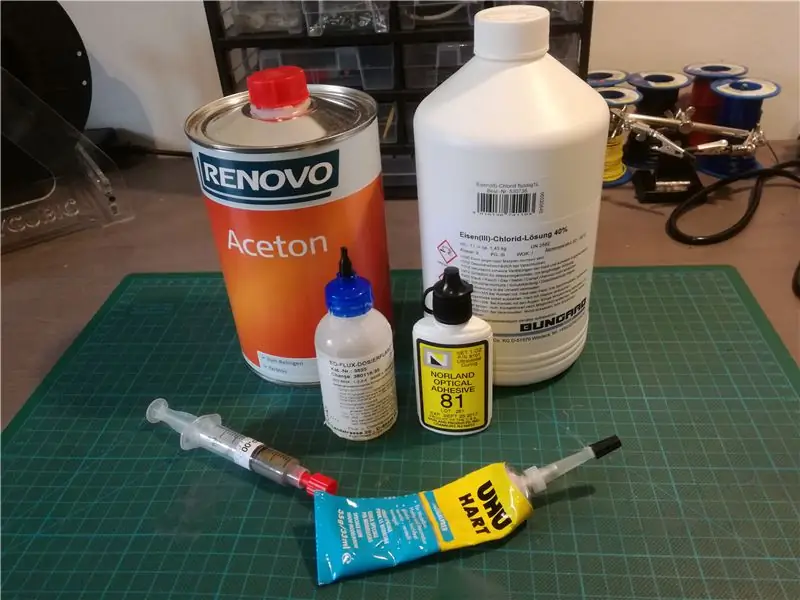
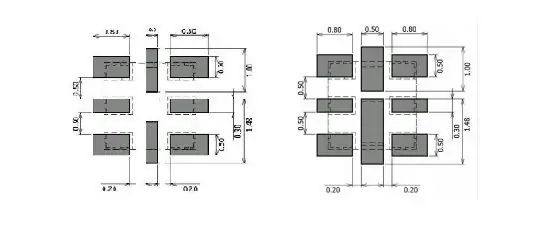
קוביית ה- LED מורכבת מכמה חומרים בלבד כמפורט להלן
- שקופיות מיקרוסקופ (25.4 x 76.2 x 1 מ"מ), למשל amazon.de
- סרט נחושת (0.035 x 30 מ"מ), למשל ebay.de
- נוריות מיקרו DotStar (APA102-2020), למשל adafruit או aliexpress
- לוח PCB אב טיפוס (50 על 70 מ"מ), למשל amazon.de
- ארדואינו ננו, למשל amazon.de
- מרווחי PCB, למשל amazon.de או aliexpress
שקופיות המיקרוסקופ ישמשו מצע עבור ה- PCB. החלטתי לחתוך אותם לחתיכות מרובעות בגודל 25.4 על 25.4 מ"מ. רדיד הנחושת צריך להיות דק מספיק לצריבה, בעוד שמילי (0.025 מ"מ) הוא בדרך כלל הסטנדרט עבור PCB, עובי של 0.035 מ"מ עובד מצוין. כמובן שרוחב סרט הנחושת צריך להיות גדול מ- 25.4 מ"מ כדי לכסות את מצע הזכוכית. החלטתי להשתמש במנורות DotStar בחבילה הקטנה יותר של 2020. לנורות אלה יש בקר מובנה המאפשר לך לטפל בכל הלדים עם שורת נתונים אחת, כלומר אין צורך ברשומות משמרות או בשילוב של חידושים. ככל הנראה ישנם שני סוגים שונים של פריסות כריות עבור נוריות ה- DotStar (ראה לעיל). פריסת ה- PCB שעיצבתי מיועדת לזה שמוצג משמאל. תצטרך 64 נוריות לד לקוביה, הזמנתי 100 חלקים שיהיו לי כמה חלפים שיכולים לשמש גם לפרויקטים עתידיים. הכל יהיה מותקן על לוח PCB של אב טיפוס שאמור להיות גדול מספיק כך שהננו הארדואינו יתאים לו. חתכתי חתיכה קטנה יותר מלוח דו צדדי בגודל 50 על 70 מ"מ (חד צדדי גם יעבוד). מרווחי PCB ישמשו ככנים לבסיס. תצטרך גם כמה חוטים דקים לביצוע החיבורים על אב הטיפוס PCB ואולי כמה "כבלי דופונט" לבדיקה.
להכנת הקוביה תזדקקו גם לכימיקלים הבאים
- פתרון כלורי ברזל
- אֲצֵטוֹן
- דבק אפוקסי, למשל Norland NO81 או NO61
- משחת הלחמה
- שֶׁטֶף
- דבק למטרות כלליות, למשל UHU הארט
כדי לחרוט את הנחושת מצעי הזכוכית קיבלתי תמיסה של כלוריד ברזל 40% מחנות אלקטרוניקה מקומית. השתמשתי בכלוריד ברזל מכיוון שהוא זול וזמין בקלות, אולם יש כמה חסרונות וכדאי לשקול גם תחריטים אחרים כגון נתרן פרסולפט. סקירה כללית של תחריטים שונים וחסרונותיהם כלפי מעלה וחסרונות שלהם ניתן למצוא כאן. הכנתי את ה- PCB בשיטת העברת הטונר והשתמשתי באצטון להסרת הטונר לאחר התחריט. כדי להדביק את רדיד הנחושת על מצע הזכוכית אתה צריך לקבל דבק אפוקסי שקוף שהוא עמיד לטמפרטורה (בגלל ההלחמה) ובאופן אידיאלי גם עמיד בפני אצטון. גיליתי שבמיוחד קשה למצוא את האחרון, אולם רוב האפוקסיות עמידות מעט באצטון וזה מספיק למטרה שלנו מכיוון שעלינו רק לנגב בעזרתו את פני השטח. החלטתי להשתמש באפוקסי נורלנד NO81 לריפוי UV, בעיקר מכיוון שאני עובד בחברה שמוכרת את הדברים. בסופו של דבר לא הייתי מרוצה במיוחד מכיוון שהאפוקסי לא נדבק טוב מאוד למצע הזכוכית למרות שהוא מיועד במיוחד להדבקת מתכת לזכוכית. במדריך שלו CNLohr משתמש באפוקסי זה שאולי כדאי לך לשקול לחלופין. לצורך הלחמת הלדים על הלוח תצטרך משחת הלחמה, אני ממליץ על אחד עם נקודת התכה נמוכה כדי להפחית את הלחץ של הלדים והאפוקסי. אתה צריך גם לקבל קצת שטף לתיקון גשרי הלחמה. סוף סוף נצטרך קצת דבק להדבקת ה- PCB מזכוכית לבסיס. השתמשתי בדבק UHU הארט למטרות כלליות אך אולי יש אפשרויות טובות יותר.
בנוסף, תזדקק לכלים הבאים לבנייה זו.
- מדפסת לייזר
- למינציה
- חותך זכוכית
- תחנת הלחמת אוויר חם
- מלחם עם קצה קטן
יש צורך במדפסת הלייזר לשיטת העברת הטונר, מדפסת הזרקת דיו לא תעבוד כאן. השתמשתי בלמינציה להעברת הטונר לנחושת. אמנם אפשר לעשות זאת גם עם מגהץ, אך גיליתי שהלמינציה נותנת תוצאות טובות יותר. תחנת הלחמת אוויר חם מיועדת להלחמת נוריות ה- SMD, אפשר גם (ואולי יותר נוח) לעשות זאת עם פלטה חמה או תנור ריפלוקס אך עדיין ייתכן שתזדקקו לתחנת הלחמה באוויר חם לעיבוד מחדש. בנוסף, מומלץ מלחם עם קצה קטן לתיקון גשרי הלחמה וליצירת החיבורים על הלוח הבסיסי. תצטרך גם חותך זכוכית לחיתוך שקופיות המיקרוסקופ לחתיכות מרובעות.
שלב 2: הדפסת פריסת ה- PCB
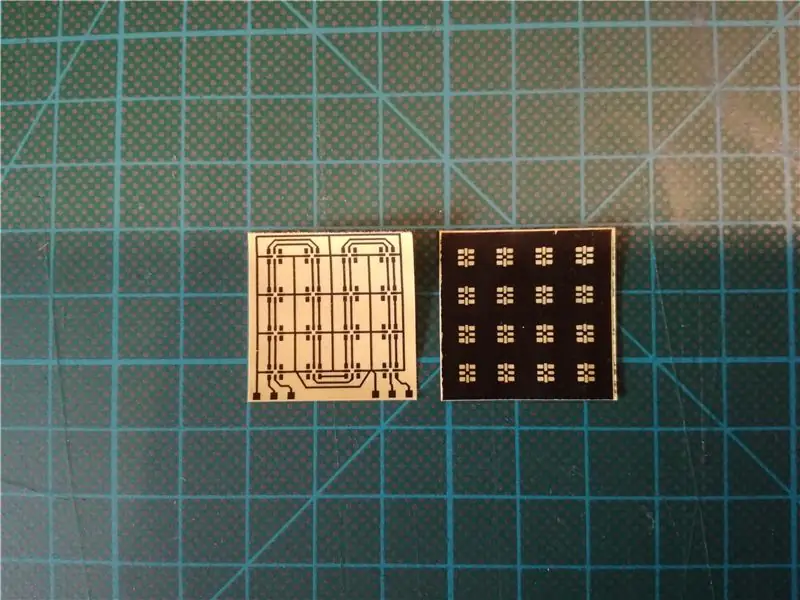
נוריות ה- DotStar יותקנו על 4 מחשבי PCB זהים, כל אחד מהם כולל מערך של נוריות 4x4. עשיתי את הפריסה של ה- PCB עם Eagle וייצאתי אותו לקובץ pdf. לאחר מכן שיקפתי את הפריסה, סידרתי כמה על דף אחד והוספתי גם כמה סימנים לחיתוך אותם לאחר מכן. ניתן להוריד קובץ pdf להלן. צירפתי גם את קבצי הנשר למקרה שתרצה לבצע שינויים כלשהם בפריסת הלוח. בנוסף, הכנתי פריסה עבור סטנסיל הלחמה שניתן לחרוט מאותו רדיד נחושת. השבלונה היא אופציונלית אך היא מקלה על הפצת משחת ההלחמה על הלוח הלוח. כפי שכבר צוין הפריסה צריכה להיות מודפסת במדפסת לייזר. אינך יכול להשתמש בנייר רגיל, אך עליך להשתמש בסוג של נייר מבריק במקום זאת. יש סוג מיוחד של נייר העברת טונר (ראה למשל כאן) אבל אנשים רבים פשוט משתמשים בנייר ממגזינים (למשל קטלוג איקאה). היתרון בנייר העברת טונר הוא שקל יותר להסיר את הנייר מהנחושת לאחר ההעברה. ניסיתי את נייר העברת הטונר הזה וגם כמה עמודי מגזינים וגיליתי שדפי המגזינים עובדים אפילו טוב יותר. הבעיה בנייר העברת הטונר שלי הייתה שהטונר לפעמים התחכך בעבר, למשל כאשר גוזרים את הפריסות הבודדות ולכן אני ממליץ להשתמש במותג אחר. במדריך שכבר הוזכר על ידי CNLohr הוא משתמש במותג זה שעשוי לעבוד טוב יותר. לאחר הדפסת הפריסות של ה- PCB וסטנסיל הלחמה גזרו אותן בעזרת סכין מדויקת. באופן עקרוני אתה צריך רק ארבע פריסות PCB ושבלונה אחת אך בהחלט כדאי שיהיו לך לפחות פי שניים מהסיכוי שכל ההעברות יצליחו.
שלב 3: הכנת נחושת על זכוכית
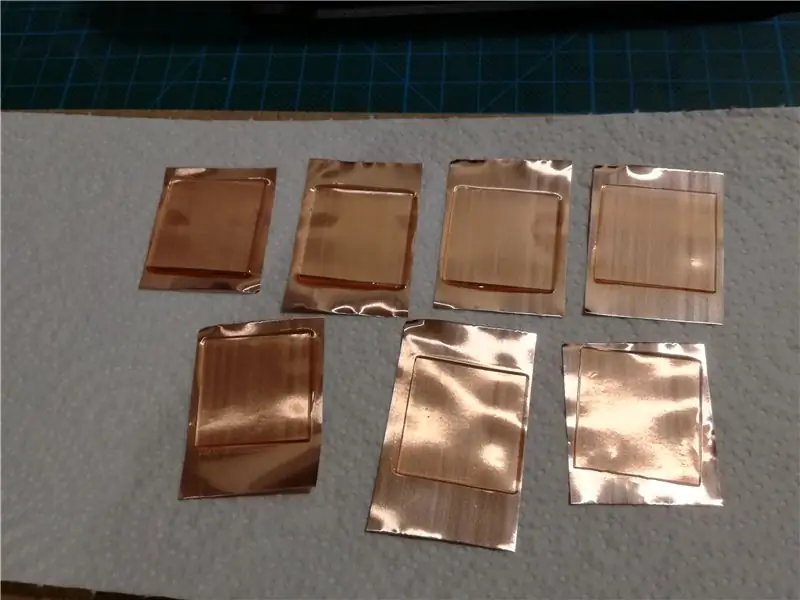
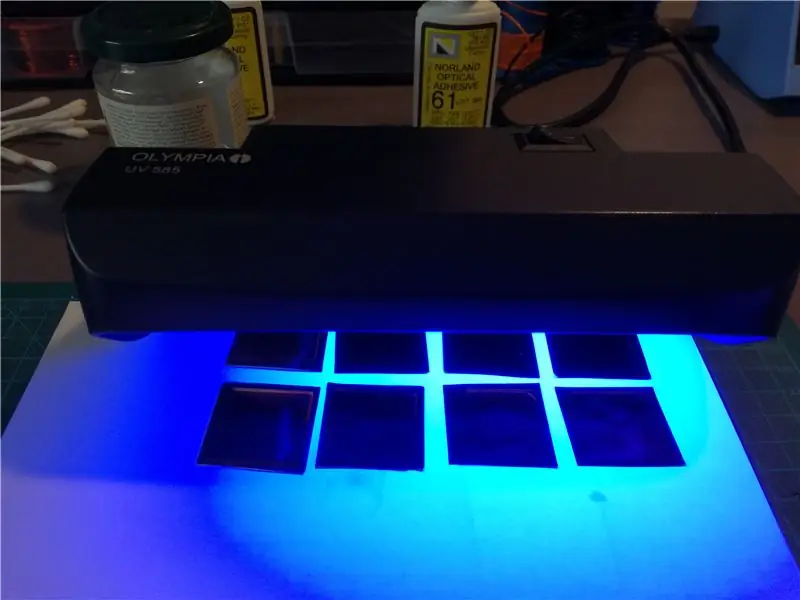
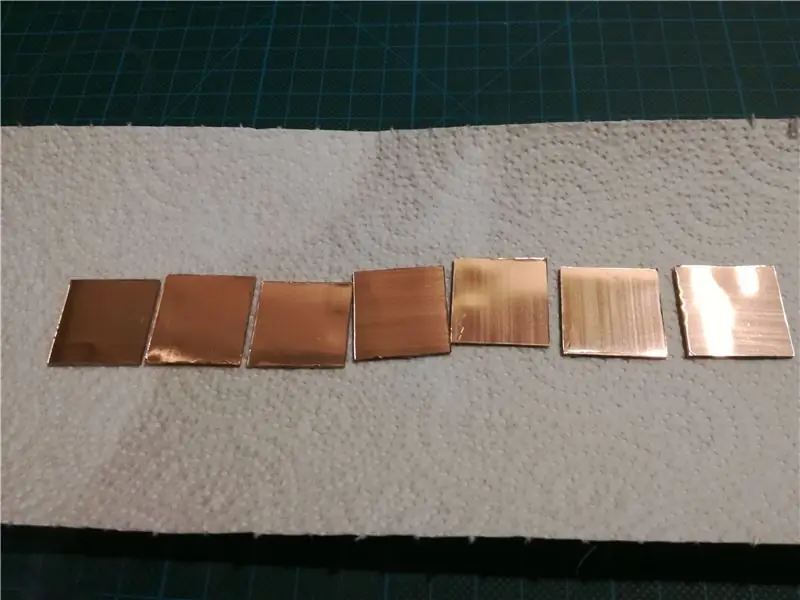
בהתחלה עליך לחתוך את שקופיות המיקרוסקופ לחתיכות מרובעות באמצעות חותך זכוכית. בנוחות אתה יכול למצוא הדרכה כמעט לכל דבר ב- YouTube. בחיפוש אחר "חיתוך שקופיות מיקרוסקופ" מצאתי הדרכה זו המראה לך כיצד היא נעשית. זה קצת מסובך לגרום לזה לעבוד כמו שצריך ובזבזתי הרבה שקופיות מיקרוסקופ, אבל אם הזמנת 100 חלקים כפי שעשיתי, יהיה לך הרבה יותר ממספיק. שוב, אני ממליץ לעשות לפחות כפול מצעים לפי הצורך (בערך 8-10) כפי שבטח תעשה כמה טעויות בדרך. לאחר מכן חותכים את סרט הנחושת לחתיכות שהן קצת יותר גדולות מצעי הזכוכית המרובעים. נקו את המצע ואת רדיד הנחושת באלכוהול או אצטון ולאחר מכן הדביקו אותם יחד. ודא שאין בועות אוויר כלואות בתוך הדבק. כפי שכבר צוין השתמשתי ב- Norland NO81 המהווה דבק מהיר לריפוי UV המומלץ להדבקת מתכת לזכוכית. עקבתי גם אחר ההוראות של CNLohr וחיספתי צד אחד של רדיד הנחושת בכדי לגרום לו להידבק טוב יותר לזכוכית. בדיעבד, סביר להניח שהייתי עושה את זה מבלי להחריף כיוון שהדבר גרם להעברת אור דרך הלוחות הלוח מעט להתפזר והייתי מעדיף שיראה בצורה ברורה יותר. בנוסף, לא הייתי מרוצה מהמידת ההדבקה של הדבק בזכוכית וגיליתי שהקצוות לפעמים מתקלפים. אני לא בטוח אם זה נבע מריפוי לא תקין או בגלל הדבק עצמו. בעתיד בהחלט הייתי מנסה כמה מותגים אחרים. לצורך ריפוי השתמשתי במנורת UV לבדיקת שטרות אשר במקרה היו שיא הפליטה באורך הגל הנכון (365 ננומטר). לאחר הריפוי חתכתי את הנחושת החופפת בעזרת סכין מדויקת. עבור סטנסיל הלחמה חתכתי גם כמה חתיכות נוספות של רדיד נחושת מבלי להדביק אותן על מצע.
שלב 4: העברת פריסת ה- PCB
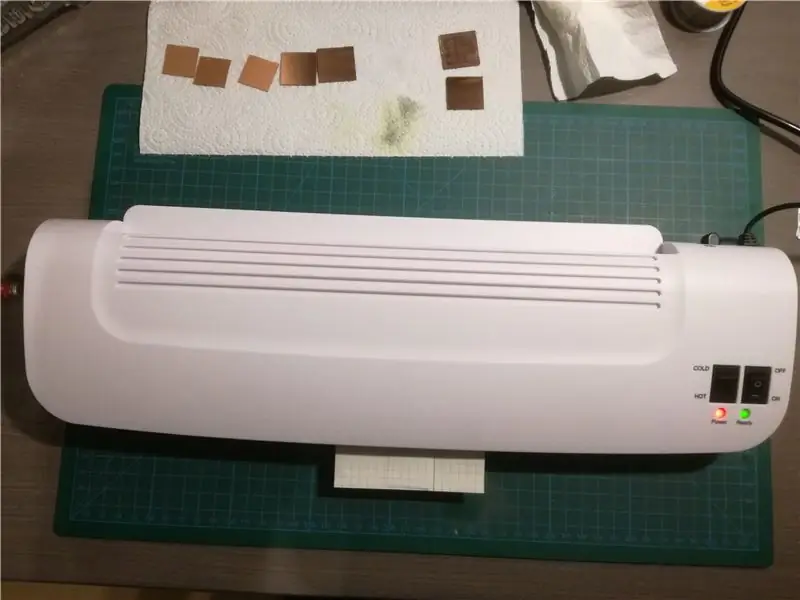
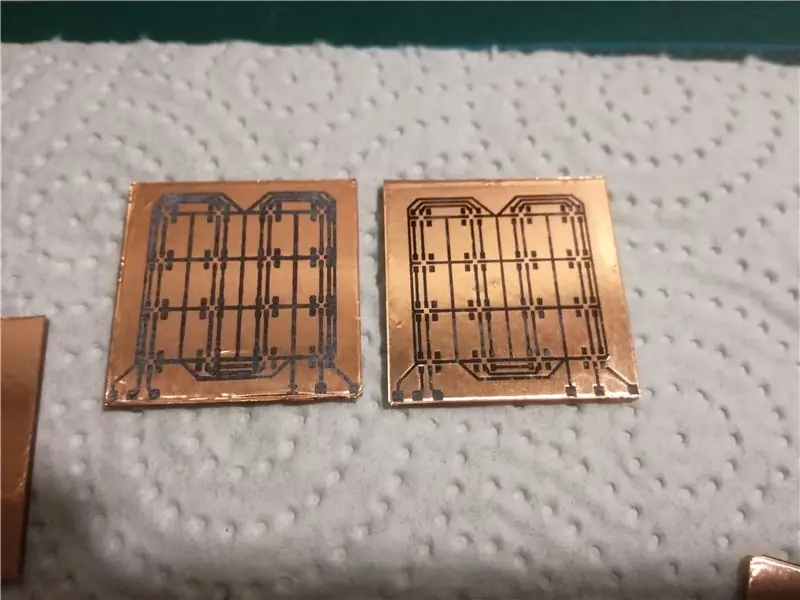
כעת יש להעביר את הטונר מהדפסת הלייזר לנחושת הנעשית על ידי חום ולחץ. בהתחלה ניסיתי את זה עם מגהץ אבל אחר כך השתמשתי במינציה. התמונה למעלה מציגה השוואה בין שתי הטכניקות לגרסה קודמת של פריסת ה- PCB. כפי שניתן לראות הלמינציה הניבה תוצאות טובות בהרבה. רוב האנשים משתמשים בלמינציה שונה שניתן לחמם לטמפרטורות גבוהות יותר. בהדרכה שלו CNLohr משתמש תחילה בלמינציה ולאחר מכן גם מחמם אותו עם מגהץ. פשוט השתמשתי בלמינציה רגילה וללא ברזל שעבד מצוין. לצורך ההעברה הנחתי את טביעת הלייזר עם הפנים כלפי מטה על הנחושת ותיקנתי אותה בעזרת חתיכת סרט דביק קטן. לאחר מכן קיפלתי אותו לפיסת נייר קטנה והעברתי אותו כ-8-10 פעמים דרך הלמינציה תוך הפוך לאחר כל ריצה. לאחר מכן הכנסתי את המצע עם טביעת הלייזר לקערת מים והשארתי אותו ספוג לכמה דקות, ואז קילפתי בזהירות את הנייר. אם אתה משתמש בנייר העברת טונר, הנייר בדרך כלל יורד בקלות מבלי להשאיר שאריות. עבור נייר המגזין נאלצתי לשפשף בעדינות חלק מהנייר שנותר בעזרת האגודל. אם ההעברה לא עבדה אתה יכול פשוט להסיר את הטונר מהנחושת עם אצטון ולנסות שוב. פריסת סטנסיל הלחמה הועברה לרדיד הנחושת החשוף באותו אופן.
שלב 5: חריטת הנחושת
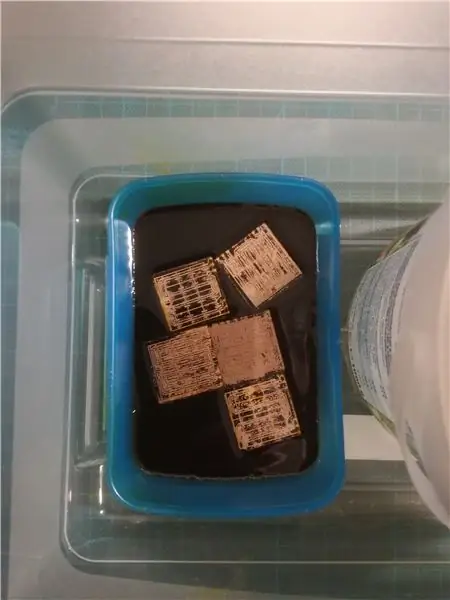
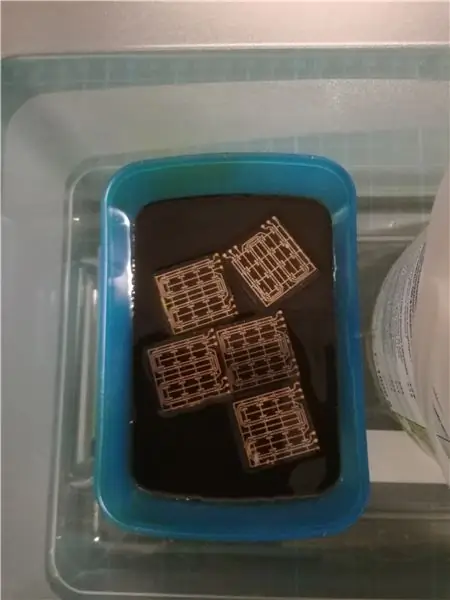
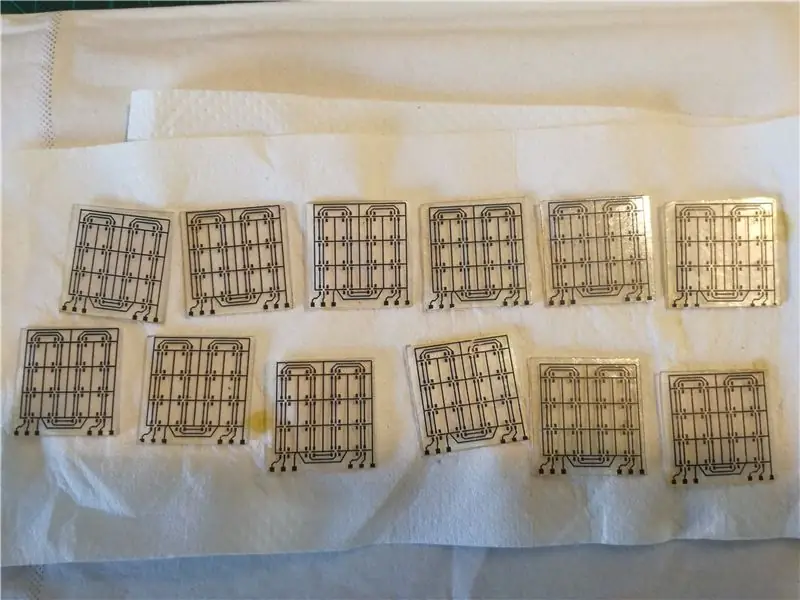
עכשיו הגיע הזמן לחרוט את הנחושת. במהלך תהליך זה הנחושת תוסר מהמצע למעט האזורים שבהם הוא מוגן על ידי הטונר. על מנת להגן על החלק האחורי של רדיד הנחושת בעזרת פריסת שבלונה של הלחמה, אתה יכול פשוט לצבוע אותו בעזרת טוש קבוע. עלי לציין שכדאי כמובן לנקוט בכמה אמצעי הגנה בעת עבודה עם תכשיר כגון חומץ כלורי. למרות שכלוריד ברזל אינו נשרף בעורך הוא יפיק לפחות כתמים צהובים-חומים, ולכן כפפות בהחלט מומלצות. כמו כן, סביר להניח שלא תופתעו מהעובדה שחומצה מזיקה לעיניכם ולכן עליכם להרכיב משקפי מגן. למיטב הבנתי, לא נוצר גז במהלך התחריט אך עדיין ייתכן שתרצה לעשות זאת באזור מאוורר היטב מכיוון שאוויר צח תמיד טוב לך;-) מלא את תמיסת החנקן לכלי קטן (אתה יכול להגן את שטח העבודה שלך מפני דליפה מקרית על ידי הנחתו במיכל גדול יותר). כאשר הכנסתי את ה- PCB, שוב עקבתי אחר ההוראות של CNLohr ושמתי את המצעים עם הפנים כלפי מטה לתוך הנוזל כך שהם יישארו צפים למעלה. זה מאוד נוח מכיוון שתדעו בדיוק מתי תסתיים התחריט, שאחרת אינכם יכולים לראות בתמיסה החומה שתחשיך עוד יותר במהלך התחריט. בנוסף, הוא גם שומר על הסעה מסוימת מתחת למצעים. מבחינתי תהליך התחריט לקח בערך 20 דקות. לאחר שכל הנחושת הלא רצויה נחרטת שטוף את ה- PCB במים וייבש אותם. אתה צריך להישאר עם כמה PCB זכוכית שקופה נחמדה. הדבר האחרון שצריך לעשות הוא להסיר את הטונר עקבות הנחושת בעזרת אצטון. פשוט נגב בעזרתו את המשטח בעדינות מכיוון שהאצטון יתקוף גם את הדבק. נא לא לשטוף את כלור החמוץ המשומש בניקוז מכיוון שהוא מזיק לסביבה (וכנראה גם יאכל את הצינורות שלכם). אסוף הכל במיכל וזרק אותו כראוי.
שלב 6: הלחמת הלדים
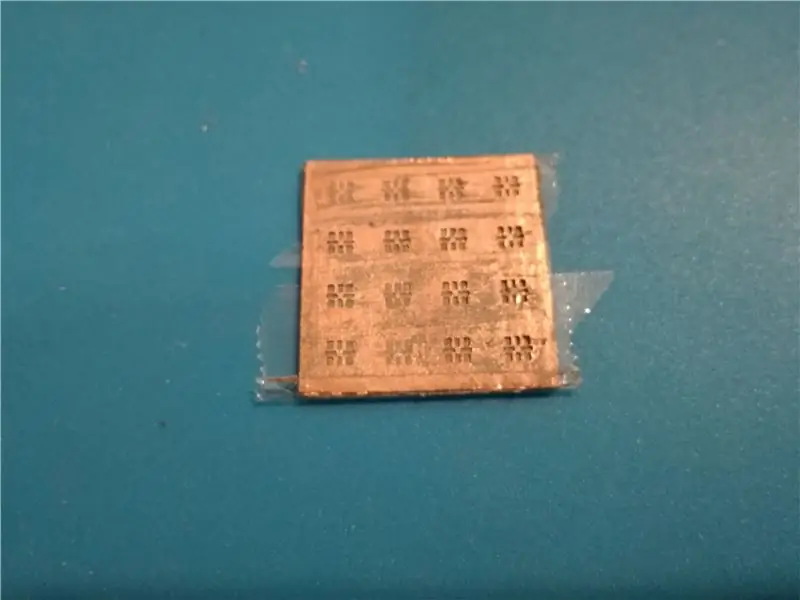
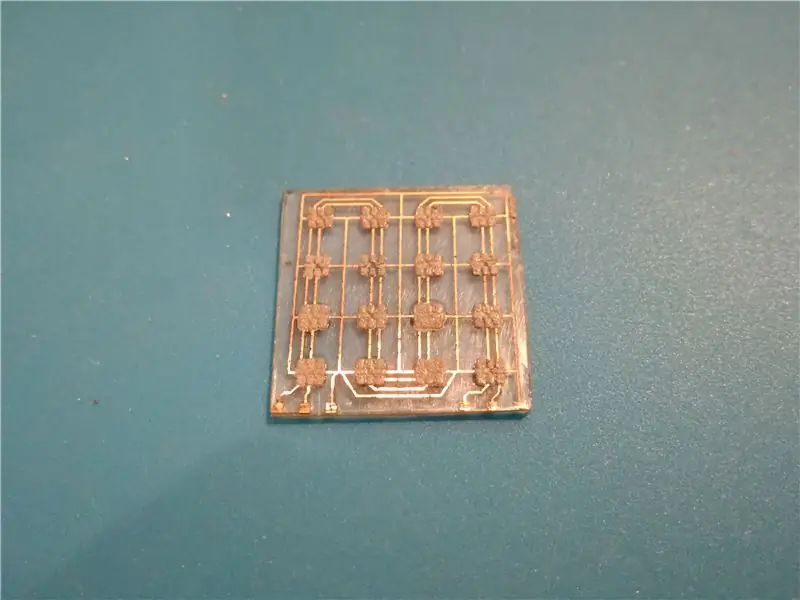
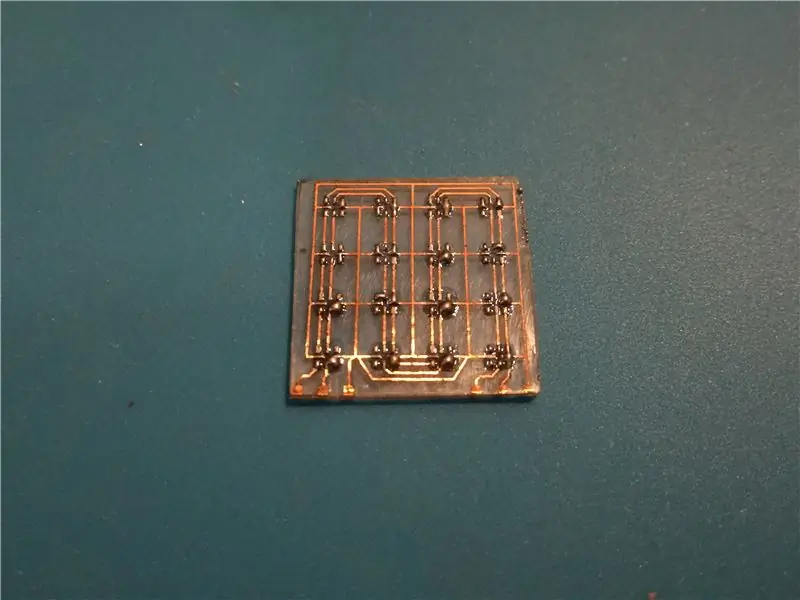
בהתאם לציוד שלך וכישורי הלחמה SMD החלק הבא עשוי להיות די זמן רב. ראשית עליך להדביק את משחת ההלחמה על הרפידות במחשב הלוח שבו הנורות יחוברו. אם יש לך חרוט סטנסיל הלחמה אתה יכול להצמיד אותו ל- PCB עם סרט דביק ואז פשוט לפזר בנדיבות את הדבק על פניו. לחלופין, אתה יכול להשתמש בקיסם כדי לשים כמויות קטנות של משחת הלחמה על כל כרית. לאחר מכן הדבר הרגיל לעשות הוא למקם את הלדים ולאחר מכן להכניס הכל לתנור מחודש (= תנור טוסטר לחובבים אלקטרוניים רבים) או על פלטה. עם זאת, גיליתי שזה בדרך כלל ייצור כמה גשרי הלחמה שקשה מאוד להסיר אותם לאחר מכן מכיוון שאינך יכול לגשת לרפידות מתחת ללדים. מסיבה זו, המיסתי תחילה את הלחמה באמצעות תחנת האוויר החם שלי ולאחר מכן תיקנתי את כל גשרי ההלחמה בעזרת מלחם באמצעות שטף וצמה להסרת הלחמה להסרת עודף הלחמה. אחר כך הלחמתי את הנורות אחת אחת עם אוויר חם. כמובן שהשיטה המהירה יותר תהיה שימוש בפלטה או בתנור, אך היתרון בשיטה שלי הוא שתוכל לבדוק את ה- PCB לאחר כל שלב. גם מבחינתי הלחמה כמעט כוללת אווירה מדיטטיבית;-). הקפד להלחם את הנורות בכיוון הנכון כפי שמוצג בסכימה למעלה. לצורך הבדיקה השתמשתי בדוגמה "בדיקת חוט" מספריית ה- DotStar adafruit וחיברתי את חוטי ה- SDI, CKI ו- GND כפי שמוצג למעלה. מסתבר שאין צורך בחיבור VCC כדי להדליק את נוריות הלדים, אך שמתי לב שהצבע האדום והכחול של הלד הראשון תמיד נדלק בו זמנית. זה לא היה המקרה כאשר VCC מחובר גם כן, אולם קשה לחבר את כל ארבעת החוטים אם יש לך רק את כמות הידיים הרגילה;-).
שלב 7: הכינו את ה- PCB הבסיסי
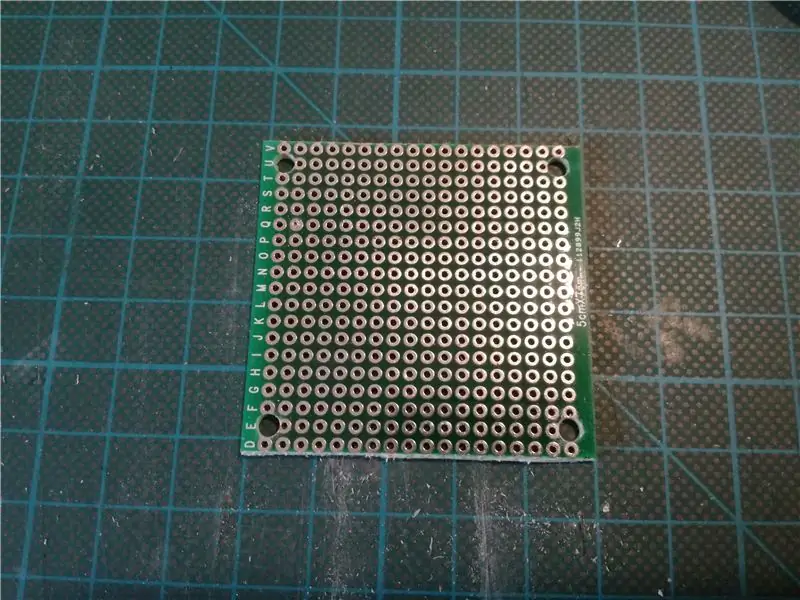
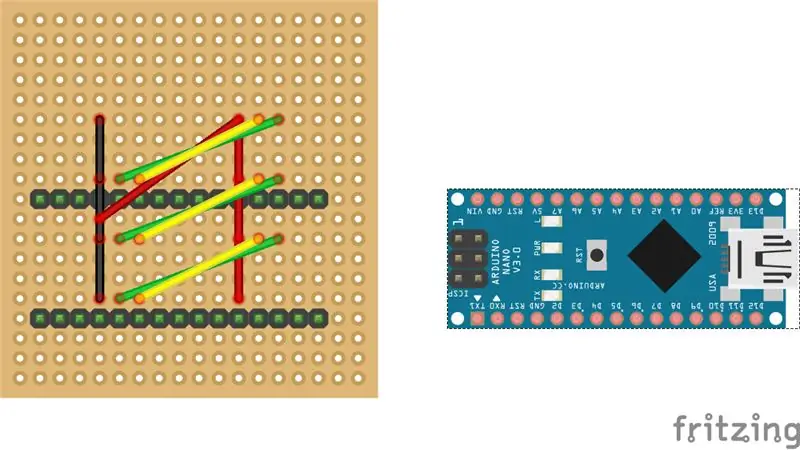
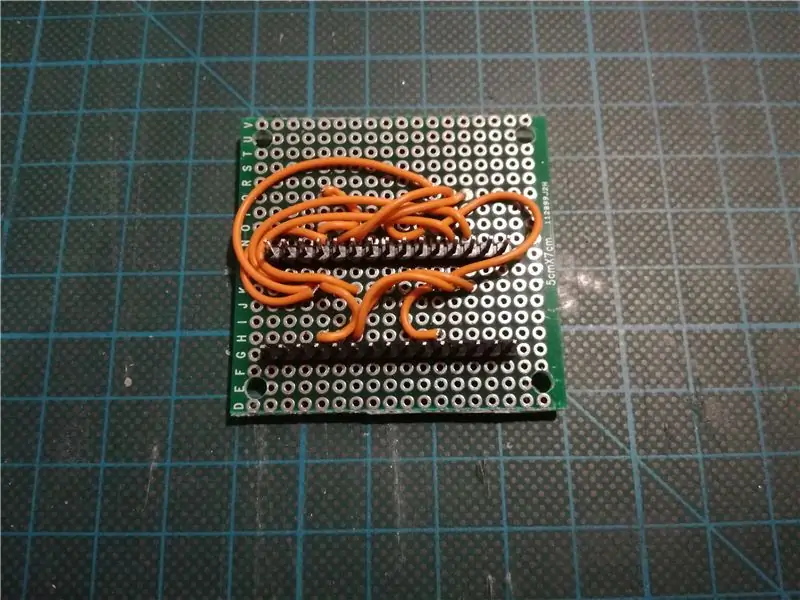
לאחר שסיימת את כל הלוחות הזכוכית עם נוריות המצורפת, הגיע הזמן להכין את הלוח התחתון שבו הם יוצבו. חתכתי חתיכה בגודל 18X19 דרך חורים מתוך אב -טיפוס PCB המספק מספיק מקום להרכבת כל הרכיבים וביצוע כל החיבורים הדרושים וגם עם ארבעה חורים שנקדחו בקצוות שבהם ניתן לחבר את מרווחי ה- PCB. אפשר להקטין את ה- PCB עוד יותר באמצעות מיקרו ארדואינו במקום ננו ארדואינו ובחירת מרווחים עם קוטר קטן יותר. הסכימה של ה- PCB מוצגת למעלה. בהתחלה אתה צריך להלחם את הסיכות של הארדואינו ל- PCB מבלי להצמיד אותן לארדואינו מכיוון שחלק מהחוטים צריכים לרדת מתחת לארדואינו (כמובן שעשיתי זאת לא נכון בפעם הראשונה). וודא גם כי הצד הארוך יותר של הסיכות פונה כלפי מטה עבור הלוח הלוח (כלומר הארדואינו יוצמד לצד הארוך יותר). לאחר מכן השתמש בחוט דק כדי ליצור את החיבורים כפי שמוצג בתרשים. כל החוטים פועלים בחלק התחתון של הלוח המודפס אך מולחמים בחלקו העליון. שים לב שאתה צריך גם ליצור ארבעה גשרים הלחמה כדי ליצור את החיבורים ל- VCC, GND, SDI ו- CKI בעזרת סיכות הארדואינו. VCC יתחבר לסיכת 5 V הארדואינו, GND ל- GND, SDI ל- D10 ו- CKI ל- D9. החיווט יצא קצת יותר מבולגן ממה שחשבתי למרות שניסיתי לסדר את הכל כך שתצטרך לעשות כמה שפחות חיבורים.
שלב 8: חבר את מחשבי הלוח הזכוכית
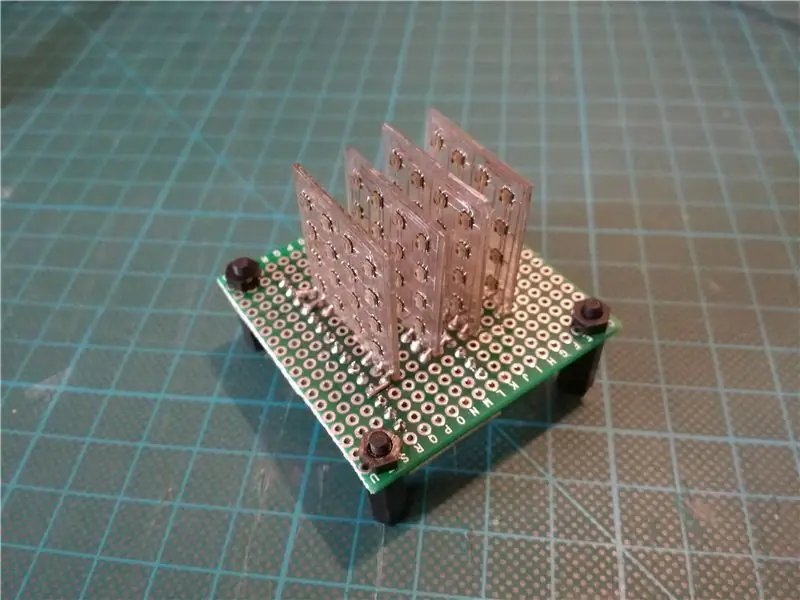
לבסוף אתה יכול לעשות את השלב האחרון של ההרכבה, כלומר חיבור מצעי הזכוכית לבסיס. התחלתי עם השכבה הקדמית הממוקמת בצד הבסיס הקרוב יותר לארדואינו. בדרך זו אתה יכול לבדוק כל שכבה לאחר הרכבה כשהאות עובר מלפנים לאחור. עם זאת, כפי שרפידות הלחמה פונות לחזית זה הופך את הלחמת השכבות האחרות למעט מסובכות מכיוון שאתה צריך להגיע ביניהן עם הלחמה שלך. כדי לחבר את הלוח, הנחתי כמות קטנה של דבק (UHU הארט) על הקצה התחתון של הלוחות הזכוכית (במקום בו נמצאים הרפידות) ולאחר מכן לחצתי אותו היטב על הבסיס וחיכיתי עד שיתקע בצורה סבירה. לאחר מכן הוספתי עוד דבק לתחתית בצד האחורי של הלוח המודרני (הפוך מכריות ההלחמה). למען האמת אני לא מאושר במאה אחוז מהתוצאה מכיוון שלא הצלחתי להרכיב את המחשבים הלוחיים בצורה אנכית בדיוק. אולי עדיף להכין סוג של ג'יג כדי להבטיח שהשכבות יישארו אנכיות עד שהדבק יתייבש לגמרי. לאחר הרכבה של כל שכבה ביצעתי את חיבורי ההלחמה על ידי מריחת כמות נדיבה של משחת הלחמה על ששת הרפידות בתחתית כך שהן מתחברות לנקודות ההלחמה המתאימות במעגל הלוח התחתון. לצורך הלחמה לא השתמשתי באוויר חם אלא במגהץ הרגיל שלי. שים לב שבשכבה האחרונה עליך לחבר רק ארבע רפידות. לאחר הרכבה של כל שכבה בדקתי את הקובייה עם קוד הדוגמה "מבחן החוט". התברר שלמרות שבדקתי כל שכבה לפני כן, היו כמה חיבורים לא טובים והייתי צריך לפתור שניים מנורות הלדים. זה היה מעצבן במיוחד מכיוון שאחד מהם היה ממוקם בשכבה השנייה והייתי צריך להגיע בין לבין עם אקדח החום שלי. לאחר שהכל עובד, הבנייה הסתיימה. מזל טוב!
שלב 9: העלאת הקוד
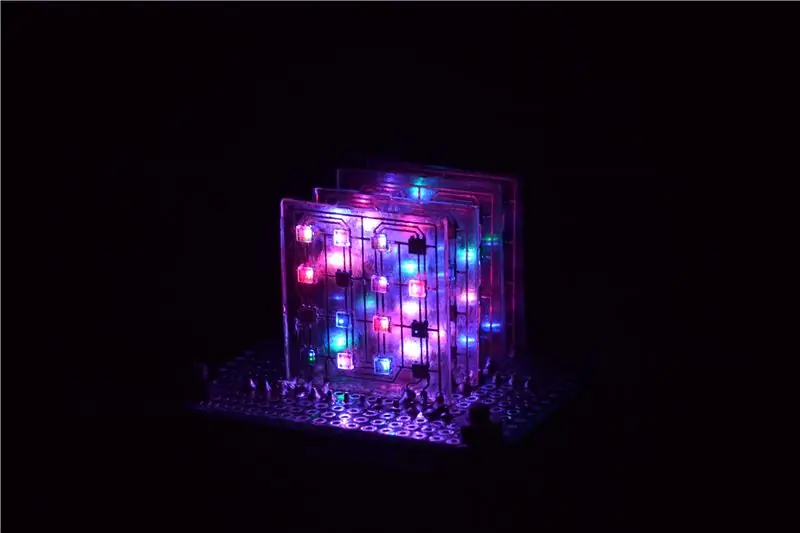
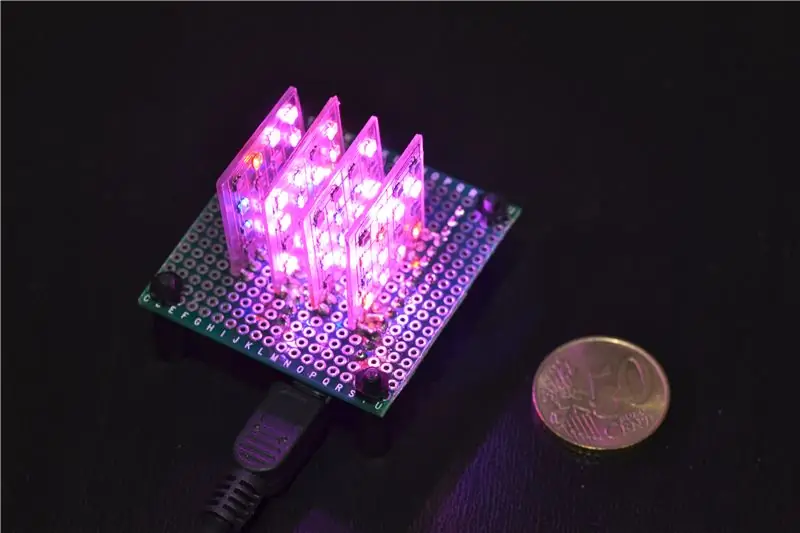
פשוט הכנתי סקיצה לדוגמא פשוטה עם כמה אנימציות שמוצגות בסרטון למעלה. הקוד משתמש בספריית FastLED והוא מבוסס על הדוגמה DemoReel100. אני מאוד אוהב את הספרייה הזו מכיוון שהיא כבר מספקת פונקציות לדהיית צבע ובהירות מה שמקל על יצירת אנימציות למראה נהדר. הרעיון הוא שתמשיך לעשות עוד אנימציות ואולי שתף את הקוד שלך בחלק ההערות. בסקיצה לדוגמה הגדרתי את הבהירות הכוללת לערך נמוך יותר משתי סיבות. ראשית, במלוא הבהירות נוריות ה- LED בוהקות באופן מעצבן. שנית, כל 64 נוריות הבהירות במלוא הבהירות יכולות למשוך הרבה יותר זרם ממה שסיכת ה 5 V של הארדואינו מסוגלת למקם בבטחה (200 mA).
שלב 10: Outlook
ישנם מספר דברים שאפשר לשפר על הבליד הזה, שאת רובם כבר הזכרתי. הדבר העיקרי שהייתי רוצה לשנות הוא הכנת לוח PCB מקצועי לבסיס. זה יאפשר להקטין את הבסיס ולהיראות נחמד יותר וגם להימנע מהתהליך המעצבן של חיווט הכל ביד. אני גם מאמין שעיצוב ה- PCB הזכוכית יאפשר מיניאטור נוסף של הקובייה כולה. בקובץ ה- LED הזעיר ביותר בעולם, nqtronix כותב כי הוא תכנן במקור להשתמש בנורות ה- RGB הקטנות בעולם בגודל 0404, אך כי לא הצליח להלחם להן חוטים. באמצעות PCBs זכוכית אפשר באמת ללכת על קוביית ה- LED הזעירה ביותר בעולם. במקרה זה כנראה שהייתי מטיל גם הכל בשרף אפוקסי הדומה לקובייה מאת nqtronix.
מוּמלָץ:
כיצד להכין קוביית LED - קוביית LED 4x4x4: 3 שלבים
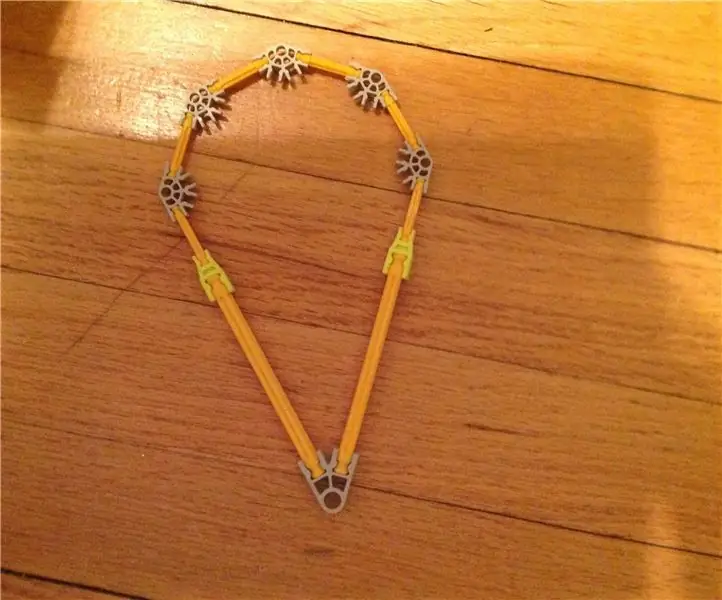
כיצד להכין קוביית LED | קוביית LED 4x4x4: ניתן לראות קוביית LED כמסך LED, שבו נוריות LED 5 מ"מ פשוטות ממלאות את תפקיד הפיקסלים הדיגיטליים. קוביית LED מאפשרת לנו ליצור תמונות ודפוסים על ידי שימוש במושג תופעה אופטית המכונה התמדה בראייה (POV). לכן
GlassCube - קוביית LED 4x4x4 על גבי PCBs זכוכית: 11 שלבים (עם תמונות)
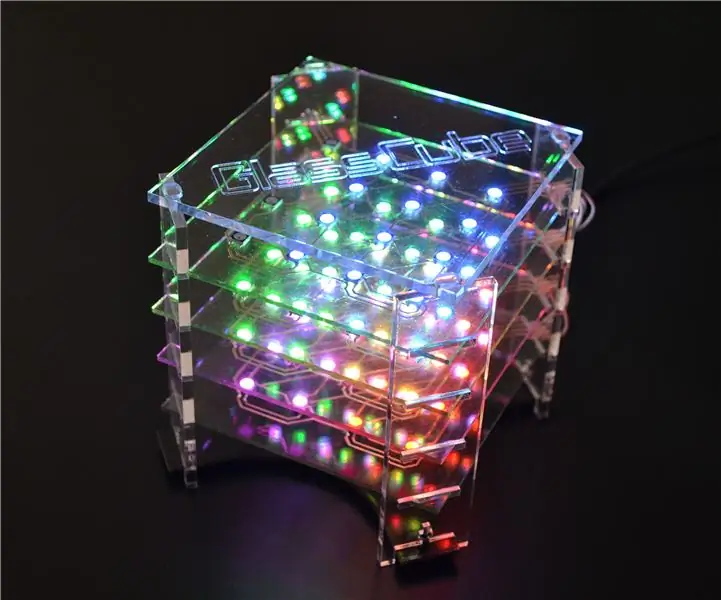
GlassCube - קוביית LED 4x4x4 על גבי PCBs זכוכית: ההוראה הראשונה שלי באתר זה הייתה קוביית LED 4x4x4 באמצעות PCB מזכוכית. בדרך כלל, אני לא אוהב לעשות את אותו פרויקט פעמיים, אך לאחרונה נתקלתי בסרטון הזה של היצרנית הצרפתית הליוקס שהשרתה אותי ליצור גרסה גדולה יותר של המקור שלי
אור אופניים בהיר מאוד באמצעות מחשבי לוח מותאמים אישית של לוח אור: 8 שלבים (עם תמונות)
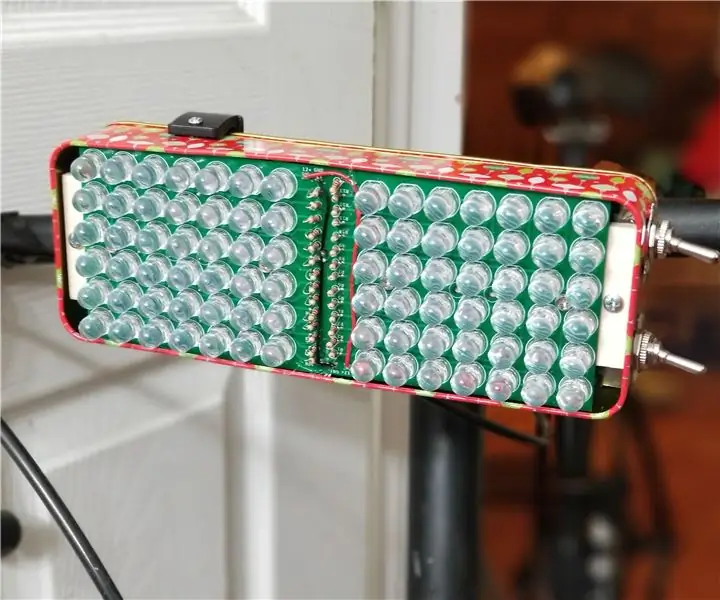
אור אופניים בהיר מאוד באמצעות מחשבי לוח מותאם אישית של לוח אור: אם אתה בעל אופניים, אתה יודע עד כמה בורות לא נעימים יכולים להיות על הצמיגים והגוף שלך. הספיק לי לפוצץ את הצמיגים אז החלטתי לעצב פנל לד משלי מתוך כוונה להשתמש בו כמנורת אופניים. כזה שמתמקד בלהיות E
כלי זכוכית זכוכית זכוכית במראה יקר למראה זול: 7 שלבים
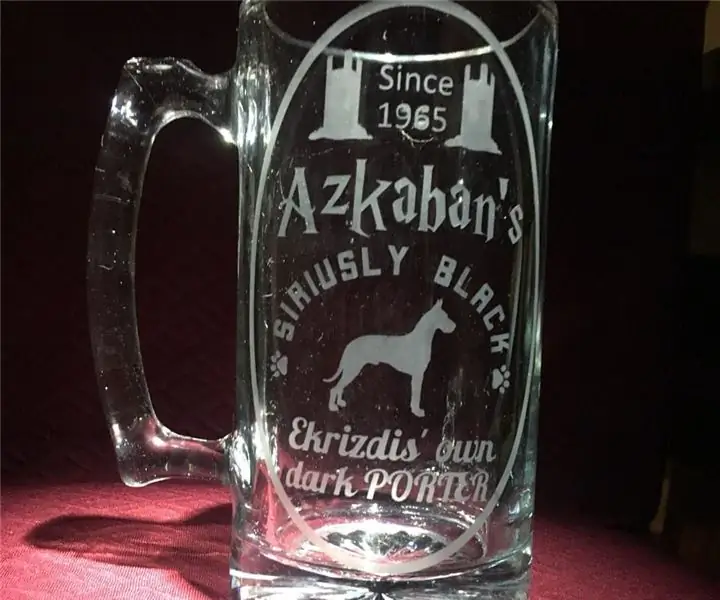
כלי זכוכית זכוכית זכוכית זולה למראה זול!: הוצא קצת $$ מראש (כ -400 $, אבל אתה יכול ללכת הרבה יותר זול (160 $) אם אתה יכול לשאול חותך ויניל), עשה הרבה על הגב (האישה ו נסעתי לבריטניה למשך 3 שבועות על הכסף שהרווחתי בזמן חלקי זה במשך תקופה של שנתיים). אני קונה
כיצד להחליף את מסך LCD זכוכית Unibody זכוכית: 7 שלבים (עם תמונות)
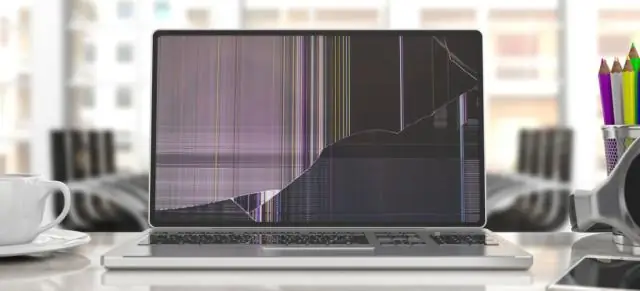
כיצד להחליף את ה- LCD של Macbook Unibody Glass: פעם זה היה שאם המסך שלך נסדק במחשב הנייד שלך, פשוט תחליף את ה- LCD ותסיים עם זה. זה לצערי כבר לא המצב. עם הצגת דגמי ה- Unibody Macbook ו- Macbook pro, שינתה אפל את עיצוב